Manage Your Perfections, Not Failures
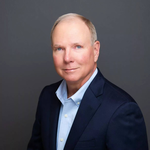
OK, maybe “perfection is too strong! How about correctness or goodness?
Please tune in this week as we discuss how the infamous Three Mile Island partial meltdown was, according to accounts, caused by a burned out light bulb, a failsafe system that would have saved the day, and how you can apply the technique of looking for goodness and correctness in your organization to inspire higher performance and strengthen your company culture.
Thank you.
Hello everyone. This is Wayne Rivers at The Family Business Institute. Thank you for tuning in.
This week, I want to talk about managing for perfection, not for failure. Let me back up already. Perfection is probably too
strong of a word. Let's say, maybe manage for goodness or manage for correctness. What does that even mean? What's
that got to do with you? All of us had moms or have moms, in my case, even though I'm 60 years old, and my mom says,
"Call me when you get there. Let me know that you arrive safely." That's managing for correctness. Moms probably didn't
know this when they started doing it, but that's managing for correctness.
The alternative would be, "Call me if something goes wrong." Well, what's the problem with that? It does make sense.
What's the problem with that? Well, it may be a really, really long time before you're able to call if something goes wrong.
If you have an accident or, even worse, you're injured, it may be a really long time before you're in a position to even be
able to call mom and say, "Oh, golly, something went terribly wrong. Can you believe it?" There is a big difference there.
There is a story, and many of you are old enough to remember this, but Three Mile Island in Pennsylvania had a partial
core meltdown in 1979. And the story may be apocryphal story but still, the story is it happened due to a burned-out light
bulb, if you can believe that. There was a safety system and when it malfunctioned, a light came on. They were monitoring
for failure. The safety system monitored and then, if something went wrong, the bulb came on and then it was an alert to
everyone to take action. Well, the bulb tried to come on, but it couldn't because it was burned out.
What would a better system? What would it look like to manage for correctness? Well, a good system would have had the
light always on and when the light went off, that's when you leaped into the action. Maybe it was just the bulb. Maybe
you have a bigger problem. That would have been a better system. The system should have been searching for perfection,
not for failure, if that makes sense.
So, for many contractors, it's the culture, it's a thankless industry. The culture is hurry up, do it faster, do it better, do it
more efficiently, make more money, et cetera, and it's a very thankless culture in construction in some ways. Contractors
kind of monitor for failure, and the industry has a reputation for kicks in the butt, more than pats on the back. And let's
face it, people of my age, that's how we were treated. It was okay in our generation. Maybe not so much now, as younger
people come into the workforce.
Wouldn't it be better in your organization to monitor for goodness, for opportunities to recognize people, to appreciate
them, to give them some praise? Wouldn't pats on the back be a better motivator than kicks in the rear end. Find ways to
celebrate ordinary behaviors and successes and emphasize them on your team. Managing for correctness, of course,
means that you need to work on your business. You need to establish a culture. You need to have codes of conduct,
operating procedures, processes, et cetera, so that once you have all that stuff in place, you can manage for perfection. If
you don't have it in place, it makes it much harder. Manage for goodness, not for failure. And I'd like to hear what you're
doing along those lines.
This is Wayne Rivers at The Family Business Institute. Thank you.