Improving Productivity: Means and Methods
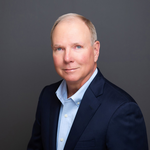
Every contractor is wrestling with the big three: inflation, supply chain issues, and the biggest of all attracting and retaining talent. Historically, the construction industry has been poor at improving productivity, but if you’re going to do more with less (the very definition of productivity), what means and methods are available to you?
Please tune in this week as Dennis makes recommendations for improving your productivity both in the office and the field. What means and methods are working for you? Please share with us in the comments section.
The Contractor Business Boot Camp class in Dallas is now more than two-thirds full. Invest in your high potential NextGen employees, and let them learn the business of construction. Please contact Charlotte at ckopp@familybusinessinstitute.com for more information.
Good morning, everybody. Dennis Engelbrecht, Digging Deeper.
Today I want to talk about productivity. My reason for talking about productivity is we're really in a very challenging time
in construction. You know, a lot of it caused just by the simple environment of the pandemic and then supply chain issues,
huge budget increases all of this. And, of course, we have the ever-present problem of a labor shortage and getting enough
people to work for.
So how do we accomplish more with less? And, of course, the answer is productivity. That's the very definition of
productivity is getting more output from fewer hours. And we're all sort of facing this challenge, it's a challenge of life and
construction does not have a great history of productivity improvement. So, I wanted to do a little analysis and maybe
break it down and figure a way that we in construction can really achieve true productivity improvement.
So, the first thing dividing productivity into something we can get our arms around. And by that I mean, it's complicated
productivity. We have means and methods, how things are actually done, the process by which things are done. We have
logistics. That's sort of the interchange of people and supply to get the things done, to have things at the right place at the
right time to do the right thing.
And then there's motivation, the people's side of it. What makes one person work a little harder, a little faster, a little
more efficiently, a little better than the next person? So, for three sessions here, I want to talk about each of these
separately to achieve our productivity improvements. So today means and methods. All right, for means and methods,
I'm very quickly reminded in my last peer group I was in, one of our owner leaders had decided that he needed to get to
the field more often and listen to what's going on out there to find out what's going on and find out how people were
feeling.
And so, he was describing a new mean and method, which they had, which was an app they had developed or adopted to
do their daily safety walkthroughs or reports. And so he went out there and started asking folks about it and folks are
telling him, "It doesn't work. It's not efficient." They weren't getting them in on time. Sometimes they went back, and they
do eight or 10 of them at once and get them in. And the overall rate of them getting in, I forget exactly what it was, but I
think it was less than 50% of the reports were actually getting done.
So, he was kind of curious as to why that was so one of the things he did was he said, "Well, let me do one of these." So,
he pulled it up and he found himself ... A pretty bright fellow, in fact one of the brightest folks I've worked with, unable to
do it. He couldn't do it. The president, owner of the company couldn't do the safety report successfully, all right. A very
simple thing, but we have a problem with means and methods. Somebody had created something, and it wasn't as easy
as they thought, didn't have the training to get folks to do it.
So, what you then have is you have frustration. You have a bad process, people aren't doing the process, the result of all
of that possible damage to the safety program, certainly frustration on people's parts, which is going to further give you
negative productivity. Because if they're frustrated versus feeling good, that's not good. So, finding the best or better way
to do each thing in your company. Now, you just think about it. This was just one process we're talking about. How many
different processes do you have in your whole company about how you're doing a form or whatever you're doing?
But there's got to be a hundred processes in your company and how many of them are actually being done the better way
or the best way? Oh, and by the way, then we have our field means and methods. So how do you get the best and better
way to do something? Well, first of all, you got to be seeking that out. Don't just do something because that's the way it's
always been done or, well, this is the way the app is designed or whatever it is. If it's not the best or better way to be doing
something, you got to be constantly seeking that best or better way.
Number two, utilize the resources and experience that you have. Now just thinking about field and job means and
methods, you probably have some folks in your organization that you might describe as complete construction
professionals. They've got it. They've got experience, they've got knowhow, they've got good decision-making. They know
more about the best and better way of doing things than other folks do, and they've had experience with it.
On the other hand, you also have A, B and C teams in your organization. And you rollout all of your jobs sometimes to an
A team, sometimes to a B team, sometimes to a C team. How do you expect the C team's going to come up with an A or
B plan and an A or B job if it's a C team without bringing in some outside expertise and help to help them do that? They
might not know the best way, the right means and methods, the better way of doing things. So, my point is you've got the
resources, you need to bring them in and apply them where they can be of use to produce the best or better way of doing
things.
Finally, there's an old saying in construction, I'm sure everybody's heard it, "Measure twice, cut once." Well, so often in
construction though we move before we have all the information. The importance to get good means and methods of
doing mock-ups, it's important. Make sure this window is framed out right,so it won't have any leaks. Well, let's do it once
instead of doing a hundred of them and then in finding out we got a problem.
So, mock-ups, doing things in prefab, the submittal and drawing reviews. These are serious things in construction. If you're
not spending time actually reviewing submittals, reviewing the drawings in detail, there are likely things in there that are
going to lead to errors and improper means and methods. So, remember to measure twice and cut once.
All right. So today, again, we brought up the subject of productivity takes means and methods, logistics, and motivation.
Today we just talked about means and methods. Find the best way to do everything you're doing in your company, bring
the right people in to make that work, make sure that you're doing the preparation steps so that you measure twice and
cut once.
Dennis Engelbrecht, Digging Deeper.